Boiler pressure gauges are critical in maintaining safe and efficient residential and commercial heating systems operations. These gauges are designed to measure the pressure inside the boiler, providing valuable data that helps operators monitor and control the boiler’s performance. This article explores the significance of pressure gauges, their types, installation, calibration, and maintenance to ensure Read more
hot water
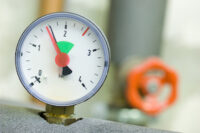
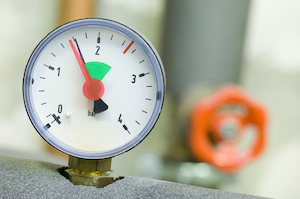
An illustration of a hot water boiler pressure gauge
Boiler pressure gauges are critical in maintaining safe and efficient residential and commercial heating systems operations. These gauges are designed to measure the pressure inside the boiler, providing valuable data that helps operators monitor and control the boiler’s performance. This article explores the significance of pressure gauges, their types, installation, calibration, and maintenance to ensure optimal and reliable functioning of boiler systems.
Importance of boiler pressure gauges
Boiler pressure gauges are indispensable components that enable operators to keep track of the pressure levels within the boiler. Maintaining the correct pressure is crucial for several reasons:
- Low-pressure indicator: One of the primary functions of the boiler pressure gauge is to indicate when the pressure in the system is too low. Low pressure often occurs due to insufficient water levels, resulting from excessive bleeding from radiators, leakages, or incomplete water filling during installation.
- High-pressure indicator: The boiler gauge also alerts users when the system pressure is too high. Radiators can be carefully bled to reduce pressure in space heating applications while monitoring the pressure gauge when the boiler is operational. In other applications, a pressure relief valve can regulate the boiler’s high pressure.
- Maintenance indication: Inconsistent pressure readings during boiler operation may indicate the need for maintenance. These irregularities could be caused by leaks, pipe blockages, or faults in the burner or electrical heating coils. When such inconsistencies are observed, it is important to conduct proper boiler maintenance to address and rectify any underlying issues.
Types of boiler pressure gauges
There are two primary types of pressure gauges used in residential and commercial boilers:
- Bourdon tube gauges: Bourdon tube gauges are the most common type in boiler applications. They consist of a coiled tube connected to the boiler system. As pressure increases, the tube straightens, and the movement is converted into a reading on the gauge. These gauges are reliable, accurate, and suitable for various pressures.
- Digital gauges: With technological advances, digital pressure gauges have become popular due to their ability to provide precise and easy-to-read pressure values. They often come with additional features like alarms and data logging, making them useful for advanced monitoring and control systems.
Selection criteria
Consider the following factors when selecting a boiler pressure gauge:
- Connection size and type: Pressure gauges come with different connections, such as BSP, NPT, and DIN.
- Connection material: Boiler pressure gauges can be made from various materials, like copper alloy and brass. It’s crucial to choose a material that is compatible with the holding socket and process. Always check the material compatibility chart before making a decision.
- Connection location: The gauge’s connection point can be located above, below, or at the rear portion of the gauge. Consider the available space in the system to make an informed decision.
- Unit of measurement: Boiler pressure gauges commonly provide readings in both bar and psi for gauge pressure measurement.
- IP protection: Considering the IP rating is important, especially if the gauge will be exposed to dust or water splashes in its environment. Higher IP ratings will increase the cost of the gauge.
- Digital reading: There are options for digital display pressure gauges, some of which can transmit readings to a remote controller. Most boiler pressure gauges have a dial indicator.
Installation of boiler pressure gauges
Proper installation is vital for the accurate functioning of pressure gauges. Key considerations include:
- Location: Install the pressure gauge on the boiler or on a nearby panel where it is easily visible to operators.
- Piping: Quality piping and fittings ensure a secure connection between the gauge and the boiler system.
- Isolation valves: Incorporate isolation valves on both sides of the pressure gauge to facilitate easy removal and maintenance without affecting the boiler’s operation.
- Calibration: Calibrate the gauge according to the boiler’s pressure range and system requirements.
Calibration and maintenance
Regular calibration and maintenance are essential to keep pressure gauges accurate and reliable:
- Calibration: Perform periodic calibration to verify the gauge’s accuracy against a standard reference. This ensures precise readings and adherence to safety standards.
- Inspection: Regularly inspect the gauge for signs of damage, wear, or leaks. Replace damaged gauges immediately to prevent inaccuracies and ensure safety.
- Cleaning: Keep the gauge lens clean and free from debris to maintain clear visibility. Replacement: Replace pressure gauges that consistently fail calibration tests or exhibit signs of malfunction.
Conclusion
Boiler pressure gauges are vital instruments that enable operators to monitor and regulate boiler pressure, ensuring safety, energy efficiency, and optimal performance. Choosing the right gauge type, proper installation, calibration, and regular maintenance are all crucial steps in maximizing the longevity and effectiveness of pressure gauges in residential and commercial boiler systems. By following these guidelines, operators can ensure safe and efficient heating operations while extending the life of their boiler systems.
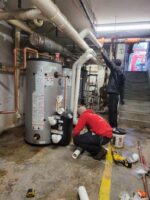
Peak Season Plumbing Problem During winter, not having hot water can be an aggravating experience for any homeowner. But if a hotel owner must deal with hot water interruption during the holiday season, the issue becomes much more disruptive and severe. A hotel in the Philadelphia area with 88 rooms faced this problem just before Read more
Peak Season Plumbing Problem
During winter, not having hot water can be an aggravating experience for any homeowner. But if a hotel owner must deal with hot water interruption during the holiday season, the issue becomes much more disruptive and severe.
A hotel in the Philadelphia area with 88 rooms faced this problem just before Christmas when its water heating system failed. Normally, plumbing contractors are used to emergency service requests, but with a snowstorm on the way, an increased number of guests and the holidays arriving, this situation required particularly quick action.
The team at Affordable Fixes Heating Cooling Plumbing completed the task by installing two HTP Phoenix tanks, with each holding a capacity of 119 gallons and 199K BTU respectively. Tackling this task required the team to remove four faulty water heaters that were leaking and generating carbon monoxide in the building.
“There are always challenges but replacing four and putting in two meant we had to put in a new exhaust, re-pipe the system, and re-do the electric units,’’ said Val Savkin, owner of Affordable Fixes Heating Cooling Plumbing. “It was supposed to be a one-day job. It took three, which was very efficient given the scope of the project.”
Due to prior communication with the building owner, Savkin knew the condition of the system. When he received a call shortly preceding he holiday season, he knew his help would be needed.
“This was an emergency project,’’ Savkin said. “The water heaters that had been in place had deteriorated. They couldn’t be repaired any longer. It was just wear and tear, they were outdated. Just two days before Christmas we were out there in the snow getting the project finalized.”
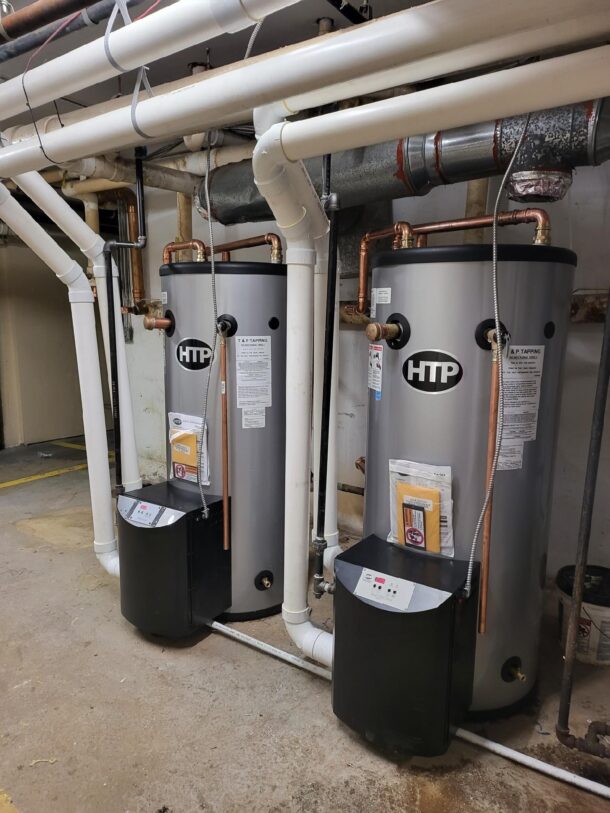
Photos by Affordable Fixes Heating Cooling Plumbing
Before Savkin chose the HTP Phoenix units, he explored other possibilities. “These HTP units were new to us, but we wanted a high efficiency, fast recovery water heater. If we had used another system, we would have to put in at least 3 units,’’ Savkin said. “We saved the customer about $12,000 by selecting this system.”
To complete the in-depth project, Savkin deployed a team of four plumbers and a debris scrapper. The initial phase involved the deconstruction and removal of the current units.
The second step proved to be just as demanding as the first step. Electrical wiring, new exhaust and gas lines were all components required for the second phase, due to the new system requiring fewer heating units.
John Monaghan, a HTP National Training Manager assisted the project by evaluating the building’s heat requirements and proposed installing two Phoenix 119-gallon tanks. “That not only saved the building owner a lot of money, but it also allowed us make the installation a little bit quicker,” Monaghan said.
Placing the tanks in the hotel’s basement was no easy task throughout the setup process. “It was a very tight fit. We were fortunate to have an elevator handy,’’ Savkin said. “We had to disassemble the new units, put them in a box, put them in the elevator and then re-assemble them. If there had not been an elevator, we would’ve gone old school and roped them down.”
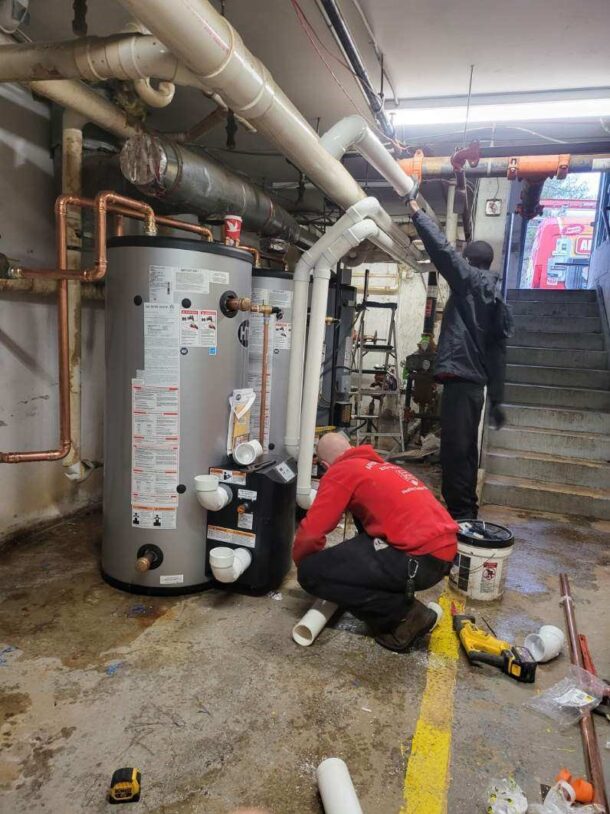
Workers from Affordable Fixes Heating Cooling Plumbing removed four water heaters and installed two HTP Phoenix 119 gallon tanks. Efficiency, durability and fast recovery factored into the decision to install the HTP products.
The selection of the HTP Phoenix water heaters was influenced by several reasons. The water heaters feature energy efficiency, durability and fast recovery that provides thermal comfort for hotel guests in a cost-effective way for the hotel owner.
“We didn’t know much about them, but we recently had training with them and I really liked their efficiency,’’ said Savkin, who has been in business in the Philadelphia area for more than three decades. “They were a great fit with a nice integrated control and easy to replace.”
Boasting a thermal efficiency rating of 96, the HTP Phoenix effectively uses 96 cents of every dollar towards heating purposes. On the other hand, a standard efficiency unit has a maximum capacity of a 60 percent efficiency rating, making the HTP Phoenix a significant upgrade. Operating at a 5:1 turndown ratio, the HTP Phoenix’s modulating burner delivers productive system efficiency even when the load is low.
To prevent corrosion, the HTP Phoenix comes with a 316L stainless steel tank. Furthermore, the unit includes a 7-year warranty for residential use and a 3-5-year warranty for commercial purposes.
“Most times you’ll get 8-12 years out of units, but like anything else it depends how much you take care of it,’’ Savkin said. “I could see these lasting 12-20 years. It’s all about the maintenance of the equipment, but it’s important to look at the water quality, too. The hardness and chemicals of the water has a lot to do with the longevity of the system.”
Receiving emergency service requests is typical for many plumbers, including Savkin. Having no access to heat or cold water will irritate any hospitality owner or homeowner, particularly during peak season.
“When we first looked at this project, we gave the owner a price and he didn’t get back to us right away,’’ Savkin said. “Then he called back and said he needed to have it done immediately. It’s an occupied hotel, and we are right around the corner. With the snow, the holidays and people traveling, this could have been a bad situation for him. We were glad to help him out and fix it quickly.”
Brian Giardina writes on a wide range of trade industry topics for publications throughout the United States.
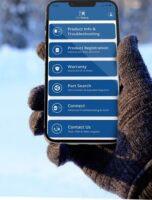
Just in time for heating season, Weil-McLain® has updated its ProTools™ App with enhanced features to provide contractors and service technicians with the support they need to streamline customer visits and provide clients with a premium experience. Available for iOS and Android devices, the app now allows heating professionals to work virtually with Weil-McLain’s Tech Support team to Read more
Just in time for heating season, Weil-McLain® has updated its ProTools™ App with enhanced features to provide contractors and service technicians with the support they need to streamline customer visits and provide clients with a premium experience. Available for iOS and Android devices, the app now allows heating professionals to work virtually with Weil-McLain’s Tech Support team to problem-solve issues as they occur on the job site.
“Our goal is to continuously optimize this platform by adding additional features that make service technicians’ and installing contractors’ jobs easier – especially during the busy heating season period,” said David DeVries, Director of Product Management with Weil-McLain. “The new Site-Call video assistance opens new opportunities for service technicians to receive instant support from our Tech Support team.”
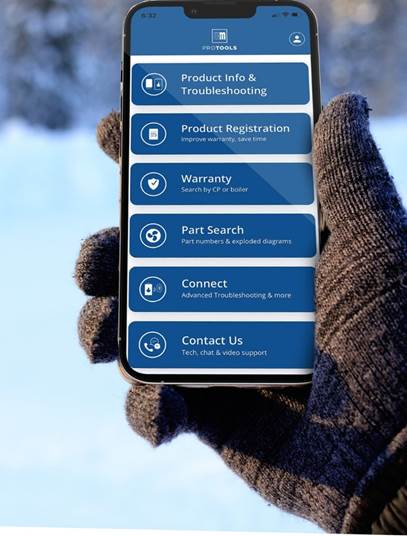
Service technicians who run into complications while on the job can contact Weil-McLain Tech Support for Site-Call video and receive immediate real-time assistance. After requesting support, they simply accept the call from Tech Support on their smartphone and share a live video of the issue they are experiencing on the job site. Tech Support will then highlight the issue on the service technician’s screen and propose corrective action to solve it.
“This new feature provides heating professionals with immediate access to our support team and also allows them the opportunity to learn new methods for troubleshooting, maintenance and boiler setup,” added DeVries. “As we prepare for what could be another colder than normal winter, we want to ensure service technicians have all the digital tools and knowledge they need to help expedite customer visits while providing homeowners a best-in-class service experience.”
The Weil-McLain ProTools App helps enhance service technicians’ hydronic expertise by putting a variety of Weil-McLain boiler product information at their fingertips. From reviewing fault codes for troubleshooting and accessing how-to videos to viewing product manuals and schematics and quickly finding parts, the app has become a one-stop resource for boiler installation and maintenance.
For more information on the upgraded Weil-McLain ProTools App, visit www.weil-mclain.com or download the app via the App Store or Google Play.
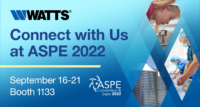
Watts will unveil solutions for a Safer, More Sustainable World at the American Society of Plumbing Engineers’ (ASPE) Convention & Expo, September 16-21, in Indianapolis, IN. Watts representatives will be on hand in Booth #1133 to discuss solutions supporting sustainability in the areas of heating and hot water, drainage, backflow & mixing, data centers, and Read more
Watts will unveil solutions for a Safer, More Sustainable World at the American Society of Plumbing Engineers’ (ASPE) Convention & Expo, September 16-21, in Indianapolis, IN.
Watts representatives will be on hand in Booth #1133 to discuss solutions supporting sustainability in the areas of heating and hot water, drainage, backflow & mixing, data centers, and water management. They will represent such brands as AERCO, BLÜCHER, Lync, ORION, POWERS, PVI, The Detection Group, and Watts.
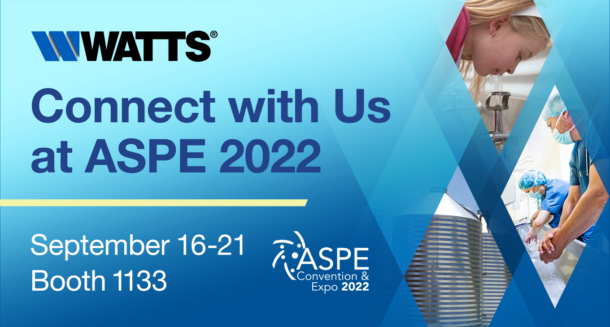
Watts experts will also be featured speakers at two technical sessions:
- David Desjardins, Business Development Manager-Mixing, Wholesale East, will present Smarter, Safer, Hot Water (Track: Codes and Standards/Water Quality) on September 20 from 8:30–9:45 am.
- Laurie Conner, President, The Detection Group, will present Wireless Water Leak Detection Systems for Commercial Applications (Track: System Design) on September 21 from 10:00–11:15 am.
For more information and to register for the ASPE Convention & Expo, go to: 2022 ASPE Convention & Expo – September 16-21, 2022 .
MILWAUKEE, Wis.—A. O. Smith, a Milwaukee-based manufacturer of residential and commercial water heaters, boilers and water treatment products, announced the beginning of its plans for integrating their most recent acquisition into its North American Water Treatment (NAWT) division. NAWT includes A. O. Smith branded water filtration and softening products, Aquasana based in Austin, Texas, Hague Read more
MILWAUKEE, Wis.—A. O. Smith, a Milwaukee-based manufacturer of residential and commercial water heaters, boilers and water treatment products, announced the beginning of its plans for integrating their most recent acquisition into its North American Water Treatment (NAWT) division. NAWT includes A. O. Smith branded water filtration and softening products, Aquasana based in Austin, Texas, Hague Quality Water based in Columbus, Ohio, and Water-Right based in Appleton, Wisconsin, and acquired by A. O. Smith in April of 2019.
Sam Karge, a Senior Vice President at A. O. Smith and President of NAWT, outlines his excitement for the collaboration within the division.
“These are truly bright, new ideas that have come out of our discussions as a team. Every company that has been brought together to form NAWT has a reputation for innovation and combining our teams is just one more innovative way that we can better serve our customers.”
Luke Java, the Director of Sales & Marketing for Water-Right, Inc., will assume the role of managing the Hague Quality Water regional sales personnel in addition to the Water-Right regional sales personnel. This move will create a central point of leadership for both sales and marketing teams, allowing better allocation of resources and providing even stronger customer support coverage.
The former sales manager for Hague, Jared Camacho, will be shifting his efforts to become the national manager of water softener Retail Sales Accounts, reporting to the Vice President of Sales and General Manager of Indirect Sales for A. O. Smith. This role will manage and further expand the retail market channel in North America.
Erik Koglin, formally the Field Manager of the Clear Choice Water Group at Water-Right, will now assist in managing the dealer networks for both Water-Right and Hague as a National Channel Manager. As the NAWT members begin to become more integrated, the role of the National Channel Manager will become important in facilitating coordination among the variety of branded dealerships within specific regions across the country. All of the dealer’s independently owned businesses dedicated to these branded networks will continue to operate as usual.
Kevin Osborn, the northeast Regional Sales Manager for Water-Right, will be taking on the role of account manager for Hague dealers in the New England territory. This will fill a formerly vacant role in the area while working to facilitate efforts between Water-Right and Hague dealers in that area.